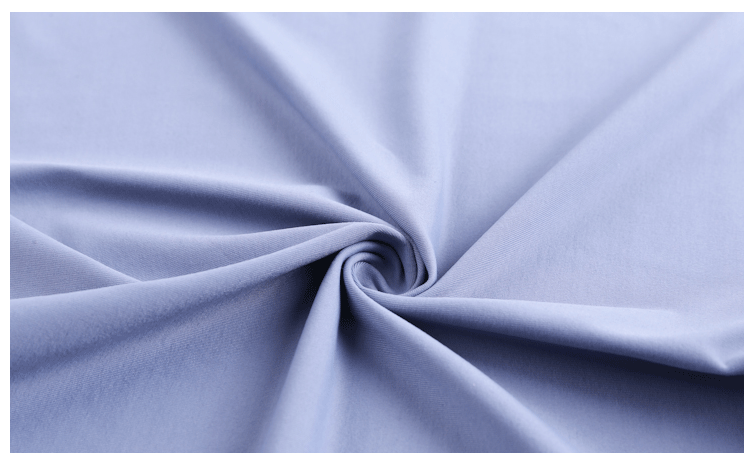
一. 基本整理
拉幅整理是利用纤维素、蚕丝、羊毛等纤维在潮湿条件下所具有的可塑性,将织物幅宽逐渐拉阔至规定尺寸并进行烘干,使织物形态得以稳定的工艺过程,故也称定整理。织物在整理前的一些加工如练漂、印染等过程中,经常受到经向张力,迫使织物的经向伸长,纬向收缩,并产生其他一些缺点,如幅宽不匀、布边不齐、手感粗糙、平带有极光等。为了使织物具有整齐划一的稳定门幅,同时又能改善上述缺点并减少织物在服用过程中的变形,一般织物在染整加工基本完成后,都需经拉幅整理。预缩是用物理方法减少织物浸水后的收缩以降低缩水率的工艺过程。织物在织造、染整过程中,经向受到张力,经向的屈曲波高减小,因而会出现伸长现象。而亲水性纤维织物浸水湿透时,纤维发生溶胀,经纬纱线的直径增加,从而使经纱屈曲波高增大,织物长度缩短,形成缩水。当织物干燥后,溶胀消失,但纱线之间的摩擦牵制仍使织物保持收缩状态。机械预缩是将织物先经喷蒸汽或喷雾给湿,再施以经向机械挤压,使屈曲波高增大,然后经松式干燥。预缩后的棉布缩水率可降低到1%以下,并由于纤维、纱线之间的相互挤压和搓动,织物手感的柔软性也会得到改善。毛织物可采用松弛预缩处理,织物经温水浸轧或喷蒸汽后,在松弛状态下缓缓烘干,使织物经、纬向都发生收缩。织物缩水还与其组织有关。织物的缩水程度常用缩水率来考核。改变纤维原有的成分和结构,提高其回弹性,使织物在服用中不易折皱的工艺过程称为防皱整理。主要用于纤维素纤维的纯纺或混纺织物,也可用于蚕丝织物。防皱整理的发展大致分为三个阶段:1)20世纪50年代中期以前,脲醛初缩体的防皱整理主要用于粘胶纤维织物,使其尺寸稳定,缩水率降低。2)20世纪50年代中期到60年代中期,美国开始生产免烫棉织物,该织物在干、湿状态下都有良好的防皱性。在此期间还出现了不少新的整理剂。3)20世纪60年代中期以后,出现了耐久压烫整理。整理的产品多为涤纶与棉的混纺织物,经成衣压烫以后,对合成纤维起热定形作用,因此在服用中能保持平挺和褶裥。织物防皱整理后,回复性能增加,一些强度性能和服用性能等得以改善。如棉织物的抗皱性能和尺寸稳定性有明显的提高,易洗快干性能也可获得改善,虽然强度和耐磨性能会有不同程度的下降,但在正常的工艺条件控制下,不会影响其穿着性能。粘胶织物除抗皱性能有明显提高之外,其断裂强度也稍有提高,湿断裂强度增加尤为明显。但防皱整理对其他相关的性能有一定的影响,如织物断裂伸长有不同程度的下降,耐洗涤性随整理剂而不同,染色产品的水洗牢度有所提高,但有些整理剂会降低某些染料的日晒牢度。热定型是使热塑性纤维及其混纺或交织物形态相对稳定的工艺过程,主要用于受热后易收缩变形的锦纶或涤纶等合成纤维及其混纺物的加工。热塑性纤维的织物在纺织过程中会产生内应力,在染整工艺的湿、热和外力作用下,容易出现褶皱和变形。故在生产中(特别是湿热加工如染色或印花),一般都先在有张力的状态下用比后续工序微高的温度进行处理,即热定型,以防止织物收缩变形,以利于后道加工。此外,利用热定型工艺并结合其他物理或机械作用还可以制得弹力纱(丝)、低弹纱(丝)和膨体纱等纱线。经过热定型的织物,除了提高尺寸稳定性外,其他性能也有相应变化,如湿回弹性能和起毛起球性能均有改善,手感较为硬挺;热塑性纤维的断裂延伸度随热定型张力的加大而降低,而强度变化不大,若定型温度过高,则两者均显著下降;热定型后染色性能的变化因纤维品种而异。利用光的补色原理增加纺织晶白度的工艺过程称为增白整理,又称加白。经过漂白的纺织品仍含有微黄色的物质,加强漂白会损伤纤维。运用增白剂能使蓝色和黄色相补,在对纤维无损伤时可提高纺织品的白度。增白方法有上蓝和荧光两种。前者在漂白的织物上施以很淡的蓝色染料或颜料,借以抵消黄色,由于增加了对光的吸收,织物的亮度会有所降低而略显灰暗。而荧光增白剂是接近五色的有机化合物,上染于织物后,受紫外线的激发而产生蓝、紫色荧光,与反射的黄光相补,增加织物的白度和亮度,效果优于上蓝。荧光增白也可以结合漂白、上浆或防皱整理同浴进行。轧光整理是利用纤维在湿热条件下的可塑性将织物表面轧平或轧出平行的细密斜线,以增进织物光泽的工艺过程。轧光机由若干只表面光滑的硬辊和软辊组成。硬辊为金属辊,表面经过高度抛光或刻有密集的平行线,常附有加热装置。软辊为纤维辊或聚酰胺塑料辊。织物经过更、软辊组合轧压后,纱线被压扁,表面平滑,光泽增强,手感硬挺,称为平轧光。织物经两只软辊组合轧压后,纱线稍赢平,光泽柔祝,手惑柔软,矿b为软轧光。使用不同钠匠辊组合和压力、温度、穿引方式的变化,可得到不同的光泽。轧光整理是机械处理,其织物光泽效果耐久性差,如果织物先浸轧树脂初缩体并经过预烘拉幅,轧光后可得到较为耐久的光泽。利用纤维的可塑性,以一对刻有一定深度花纹的硬、软、凹、凸的轧辊在一定的温度下轧压织物,使其产生凹凸花纹效果的工艺过程称为轧纹整理,又称轧花整理。染色或印花后的棉或涤/棉混纺织物,在轧纹整理中若浸轧树脂工作液,可形成耐久性的轧纹效果。合成纤维织物染色印花后可直接进行轧纹。以刻有凹纹的铜辊作硬辊,以表面平整的高弹性橡胶辊作软辊轧压织物的工艺,便称拷花。用砂磨辊(或带)将织物表面磨出一层短而密的绒毛的工艺过程称为磨绒整理,又称磨毛整理。磨毛织物具有厚实、柔软而温暖等特性,可改善织物的服用性能。变形丝或高收缩的涤纶针织物或机(梭)织物磨毛后,能制成一种仿麂皮绒织物。以超细合成纤维为原料的基布,经过浸轧聚氨酯乳液和磨毛,可获得具有仿真效果的人造麂皮。磨毛(或磨绒)整理的作用与起毛(或拉绒)原理类似,都是使织物表面产生绒毛。不同的是,起毛整理一般用金属针布(毛纺还有用刺果的),主要是织物的纬纱起毛,且茸毛疏而长。磨绒整理能使经纬纱向同时产生绒毛,且绒毛短而密。磨绒整理要控制织物强力下降幅度,其质量以绒毛的短密和均匀程度为主要指标。
三 . 如何控制纺织品染色大货与小样之间的色差
在实际生产中,染色大小样完全无差异是不可能的,应采取有效方法予以纠正。现将常用解决方法简述如下:棉及其混纺交织物中,棉组分经直接染料或活性染料染色后,出现浮色或色泽萎暗,一般采取继续水洗,或在水洗浴中添加0.5-1L防沾色清洗剂水洗。若水质硬度偏高,可加入0.5~2g/L的螯合分散剂加以改善。忌用混浊的江河水或硬度较高的深井水。涤纶混纺交织物染色时,所用染料和助剂品种多,可采取40℃水洗,以利于沾染到织物上的残留物溶落。纤维素纤维采用直接混纺染料染色,若大样整体得色比小样深一些,经温水洗一遍后得色即可相近,在一定程度还能提高色牢度。热水清洗大多用于酸性、直接和碱性染料染色的丝绸或合纤及其交织物。若得色偏深,需去除染物1~2成的染料,可采取70~80℃热水洗。丝织物热水洗浴中可添加0.3~0.5L的平平加0(匀染剂);涤纶、锦纶等合纤混纺交织物,则可加人0.5~1.0L的修补剂或染色载体。由于热洗浴中添加的助剂量少,织物只需用流动水洗至室温即可。如染色织物采用阳离子固色剂和柔软剂等处理,最好在热洗浴中追加2~4L分散剂DAM。热水洗(修复)原则上在原染色设备上进行,如尼丝纺、醋酯纤维及其交织绸类卷染后,若改用溢流机(绳状)热水洗,会使织物产生永久折皱。(1)用直接染料染纤维素纤维,染色大样深度往往不够。若染浴中尚有染料,可追加1.5—5.Og/L电解质(NaCl、Na2SO4)促染。这对盐效应直接染料,如直接耐晒黄3RLL、橙(L、大红BNL、红4BL、红玉RNLL、紫BL、蓝BL、B2RL、天蓝G、翠蓝GL、绿5GLL、绿GL、灰4GL、灰GB等十分有效。对于温度效应直接染料,则还需保持一定温度。(2)用酸性染料染蛋白质纤维,或用碱性染料或阳离子染料染腈纶,染色大样出现颜色过深或色花时,可追加3~6g/L Na2SO4,予以褪色或匀染。(1)用酸性染料染蚕丝、羊毛等蛋白质纤维,如染色大样偏浅而染液中尚有余色时,可追加O.5—2mL/L的98%醋酸促染。追加前必须关闭蒸汽阀,用1O倍冷水稀释后,在染物运转时缓慢加入,以避免造成新的色花。(2)用K型和KN型活性染料染纤维素纤维,若大样偏深,可追加2—3mL/L的98%醋酸,于90—95℃处理3Omin,促使染料部分断键而消色,一般可减浅20%左右。(3)用碱性染料染丝绸或用阳离子染料染腈纶时,若大样偏深,可采用2~3mI/L醋酸,在4JD一60℃的温水浴中处理2O~30min,使染料溶解而减浅20%~30%。(1)用分散染料染涤纶及其混纺交织物,大样比小样颜色深时,一般可追加高温匀染剂或修补剂。大样色浅,应追加相应的染料,但应注意追加时要关闭蒸汽阀,以避免产生色花,先加入适量的匀染剂。此外,当分散染料进行追加染色时,要升温至一定的染色温度,并保温15—20min,再降温降压及对样。(2)用直接、酸性、中性等染料染纤维素纤维、蚕丝、羊毛和锦纶织物时,原则上都可采用平平加O去除迁移染料,达到匀染。羊毛织物上平平加O的用量一般不能超过0.3g/L。为防止羊毛毡化,也可添加羊毛保护剂色乐保WOK2%一3%(Dys—tar)。用中性染料染锦纶时,若大样得色过深或有横档等需覆盖时,采用色乐高N—ER3%~5%(D'ystar)效果极佳。(3)用碱性和阳离子染料染腈纶、碱改性涤纶和蚕丝时,若染色大样颜色稍偏深,可采取热水清洗;若大样颜色深20%左右,可在染色残液基本洗尽时,加入2~4L表面活性剂1227,通过竞染作用达到褪色。染红玉、玫瑰红、紫罗蓝、雪青、天蓝和艳紫等鲜艳色时,若感觉大样不够亮丽,一般可追加0.0015%~0.0025%(owf)荧光增白剂,颜色越浅用量越少。棉纺织品以荧光增白剂4BK的效果较好,其荧光弱、艳度强、用量少、可调性好,且适应颜色广,不易“跳灯”。因荧光增白剂引起的“跳灯”,可用不影响颜色鲜艳度的荧光沾污清除剂去除。对于涤棉(粘胶)和锦棉(粘胶),由于涤和锦属疏水性纤维,其得色较棉和粘胶等亲水性纤维深,可在60℃清水浴中加入2—4mL/L染色载体,然后逐步升温至80~9O℃,使疏水性纤维上的染料缓慢解吸下来,达到两相色光一致。实践证明,染色载体不仅能溶落疏水性纤维上的分散染料,对其它染料也同样具有溶落作用。当温度升至80℃后,操作工要不断取样对样,一般保温至大小样相符。1.对涤纶追加分散染料纠色时,最好先将染浴温度降至80℃以下,再将事先溶解好的染料充分稀释,并在5~8min内加完,然后继续上升温度至原染色温度,保温染色15rnin以上,确保前后颜色均匀透染,以减少对热定形的影响。2.如果染物出缸后发现大小样色差,可在大样上追加染料或调整色光。调整时,除要计算大样上所需要的染料品种及数量外,在空白浴中也要补充原处方15%一20%的染料。3.对用3~4种染料拼成的颜色,如米灰、瓦灰、香灰、银灰和象牙白等,不能用染(颜)料修复大小样间的色差。
四 . 水洗软片在纺织品应用中的作用
①达不到应有手感:柔软整理的柔软风格随客户要求不同而不同,如柔软、平滑、蓬松、柔糯、油滑、干滑等,根据不同的风格选用不同的柔软剂。如软片中,有不同结构的柔软剂软片,其柔软度、蓬松度、滑度、泛黄情况、影响织物吸水性等均不同;在硅油中,不同改性基因的改性硅油性能也不同,如氨基硅油、羟基硅油,环氧改性硅油、羧基改性硅油等等性能均不同。
②色变泛黄:一般由一定结构软片及氨基硅油中的氨基造成泛黄。在软片中,阳离子软片柔软佳、手感好,易吸附在织物上,但易泛黄变色,影响亲水性,如将阳离子软片改制成软油精,其泛黄会大大降低,亲水性也有改善,如将阳离子软片与亲水硅油复合,或与亲水整理剂复合,其亲水性会有改善。阴离子软片或非离子软片不易泛黄,有的软片不泛黄,也不影响亲水性。氨基硅油是目前应用最广的硅油,但因氨基会造成变色泛黄,氨值越高其泛黄越大,应改用低黄变氨基硅油或聚醚改性、环氧改性等不易泛黄的硅油。另外,乳液聚合时有时采用阳离子表面活性剂如1227、1831、1631作乳化剂,这些乳化剂也会产生泛黄现象。硅油乳化时使用乳化剂不同,其“剥色效应”不同,会造成不同情况下的剥色而色浅,已属于色变。
③织物亲水性下降:一般是采用的软片结构问题及硅油成膜后缺少吸水基因,以及封闭了象纤维素纤维的羟基、羊毛上的羧基、氨基等这些吸水中心造成吸水性下降,应尽可能选用阴离子、非离子软片及亲水类型的硅油。
④深色斑:主要原因是前处理时织物油污未去净,染色时油污处色泽偏深;或染色浴中泡沫过多,泡沫与花毛衣、染料等混合物沾于织物上;或消泡剂飘油造成深色油斑;或染缸中焦油状物沾在织物上;或染料在不同情况下凝集而成深色色斑;或水质钙镁离子过多与染料结合沾于织物等原因。要针对性进行处理,如前处理时加去油剂进行精练,染色助剂采用低泡、无泡助剂,消泡剂选择不易飘油的品种,加螯合剂改善水质,加助溶分散剂防染料凝集,及时用清缸剂进行清缸洗缸。⑤浅色斑:主要原因是前处理不均匀,有些部位的毛效不佳,产生一定的拒染性,或带有拒染性物质,或前处理时布上带有钙皂、镁皂等或丝光不均匀,或半制品烘干不均匀,或布面沾上未溶解元明粉、纯碱等固体,或染色物烘干前滴上水,或染色物柔软处理等后整理时带的助剂斑渍。同样地必须针对性处理,如加强前处理,前处理助剂选择时必须不易形成钙镁皂,前处理必须均匀透彻(这与精练剂、渗透剂、螯合分散剂、丝光渗透剂等选择有关),元明粉、纯碱等必须化好进缸而且必须加强生产管理工作。
⑥碱斑:主要原因是前处理(如漂白、丝光)后去碱不净或不均匀,造成碱斑产生,所以必须加强前处理工序的去碱工艺。⑦柔软剂渍:造成原因大概有以下几种:
a.软片化料欠佳,有块状柔软剂粘附于织物上;
b.软片化料后泡沫太多,在布匹出缸时,布带上柔软剂泡沫渍;
c.水质不佳,硬度太高,水中杂质与柔软剂结合凝集在织物上。甚至有的厂用六偏磷酸钠或明矾等处理水,这些物质与水中杂质形成絮状物,进入柔软处理浴后使布面带斑渍;
d.布面带阴离子物质,在柔软加工时,与阳离子柔软剂结合成渍,或布面带碱,使柔软剂凝聚;
e.柔软剂结构不同,有的在较高温度下造成柔软剂从乳化状态变成渣状物粘附于织物等等。
f.缸中原有焦油状柔软剂等物质掉下粘在织物上。
⑧硅油斑渍:这是最难处理的一类斑渍,主要原因:
a.布面PH值未达中性,特别是带碱,造成硅油破乳飘油;
b.处理浴水质太差,硬度太高,硅油在>150PPM硬度的水中极易飘油;
c.硅油质量问题包括乳化欠佳(乳化剂选择欠佳、乳化工艺欠佳、乳化粒子太大等),不耐剪切(主要是硅油本身问题如硅油质量、乳化体系、硅油品种、硅油合成工艺等)。可以选择耐剪切、耐电解质、耐PH变化的硅油,但要注意硅油的使用方式及环境,也可考虑选亲水的硅油。
⑨起毛不佳:起毛不佳跟起毛机的操作(如张力控制、起毛辊转速等)有密切关系,对于起毛来说,上柔软剂(俗称上蜡)时,控制织物的动、静摩擦系数是关键,故起毛柔软剂的配制是关键,如果柔软剂用的不佳,会直接造成起毛不佳,甚至造成布拉破或门幅变化。
2 树脂整理中常见的质量问题:
①甲醛问题:由于树脂中的游离甲醛或N—羟甲基结构的树脂分解出的甲醛造成甲醛含量超标。宜采用超低甲醛树脂或无甲醛树脂。当然甲醛问题的来源很广泛,如固色剂Y、M,柔软剂MS—20、S—1,防水剂AEG、FTC,粘合剂RF,阻燃剂THPC等助剂中有时也会造成甲醛超标。同时空气中的甲醛迁移也可能造成织物上甲醛超标。
②泛黄或色变问题:树脂整理后,一般会造成泛黄,所以要控制树脂整理剂的PH值、含酸成分、催化剂成分,尽可能减少泛黄、色变。
③强力下降问题:一般树脂整理均会产生强力下降,可加入纤维保护剂,如氧化聚乙烯蜡乳化体。④手感问题:一般树脂整理会造成手感变硬现象,可加入柔软成分,但要注意不能影响树脂整理质量。手感改善了,对改善强力下降问题也大有改善。但表面树脂造成的手感发硬等问题是由树脂本身及烘干等原因造成,要针对性进行改善。3 其它质量问题:
①金属离子超标:金属离子Cu、Cr、Co、Ni、Zn、Hg、As、Pb、Cd等在出口产品中有检测,如果超标,也象甲醛超标一样产生严重后果,在助剂中,这类金属离子较少,但有些助剂会造成超标,如阻燃剂三氧化二锑乳液含有大量汞,防水剂CR、Phobo Tex CR(ciba)、Cerolc(山德士)等含铬。毛纺上用媒介染料时,所用媒介染剂为重铬酸钾或重铬酸钠或铬酸钠,Cr6会超标。
②色泽变化问题:在经后整理后,色泽变化问题是较多的,这必须注意染色时染料的选择,在染色打样时,必须按工艺进行相应的后整理,判断选用的染料是否会在后整理中在助剂作用下发生色变,当然,最好选择不会造成色变的后整理剂是最理想的方案,但这往往具有局限性(如含铜的抗菌剂本身有颜色,含铬的防水剂也有颜色,会造成织物的色变),同时也要考虑到染色织物在烘干焙烘时染料升华造成的色浅和色变及温度过高造成的泛黄等因素。
③APEO超标:APEO作为一项指标也被一些国家严格限制,这个指标和前处理中的精练剂、渗透剂,印花染色中的净洗剂、匀染剂,后整理时柔软剂中的乳化剂等均相关,在目前尚广泛应用TX、NP系列表面活性剂作助剂原料的情况下,其防范有难度,唯一的道路是印染厂坚持使用环保助剂,严格杜绝含有APEO及有毒有害物质的助剂进厂使用。
五 . 涤纶和尼龙的区别与区分
特点:强度高、耐冲击性好,耐热,耐腐,耐蛀,耐酸不耐碱,耐光性很好(仅次于腈纶),曝晒1000小时,强力保持60-70%,吸湿性很差,染色困难,织物易洗快干,保形性好。具有“洗可穿”的特点
短纤:棉、毛、麻等均可混纺,工业上:轮胎帘子线,渔网、绳索,滤布,缘绝材料等。是目前化纤中用量最大的。
尼龙/锦纶(结实耐磨): 最大优点是结实耐磨,是最优的一种。且受力,色牢度,光泽度等方面均好于涤纶产品,也不易产生死皱。密度小,织物轻,弹性好,耐疲劳破坏,化学稳定性也很好,耐碱不耐酸! 最大缺点是耐日光性不好,织物久晒就会变黄,强度下降,吸湿也不好,但比腈纶,涤纶好。
用途:长丝,多用于针织和丝绸工业;短纤,大都与羊毛或毛型化纤混纺,作华达呢,凡尼丁等。工业:帘子线和渔网,也可作地毯,绳索,传送带,筛网等。
一般来说做箱包的都是尼龙牛津布,尼龙和涤纶的区别最简单的就是燃烧法!涤纶的冒很旺的黑烟,尼龙的冒白烟,还有就是看燃烧后的残留物,涤纶的捏会碎,尼龙的成塑!价格来说尼龙的是涤纶的两倍。
1、尼龙,近火焰即迅速卷缩熔成白色胶状,在火焰中熔燃滴落并起泡,燃烧时没有火焰,离开火焰难继续燃烧,散发出芹菜味,冷却后浅褐色熔融物不易研碎。
涤纶,易点燃,近火焰即熔缩,燃烧时边熔化边冒黑烟,呈黄色火焰,散发芳香气味,烧后灰烬为黑褐色硬块,用手指可捻碎。
2、手感也会不同 涤纶手感比较糙 尼龙手感很比较幼滑些
3、可以用指甲刮,指甲刮后,有明显痕迹的是绦纶,痕迹不明显的是尼龙,但是这种方法不如第一种方法直观易辩。
六 . 丝光牛仔布及其工艺简介
丝光牛仔面料在传统牛仔布生产工艺的基础上,采用新型染整加工技术,对纱线表面进行丝光,以达到表层色浓、内层洁白、对比鲜明的环染效果,其色泽鲜艳度、深度较常规纱线要好得多。丝光牛仔布以其舒适的手感、较好的光泽、鲜明的磨白效果和清晰的布面风格,赋予牛仔面料以高附加值,是高档牛仔服装的首选面料。染整工艺 坯布 4000px83.4/58.3268/181牛仔布。
工艺流程 坯检→烧毛→退浆→丝光→水洗→定形→整纬→预缩→成检→卷筒
1 烧毛 正面烧两次,车速控制在80m/min,火口要求均匀有力,火力不宜太高,尤其要注意布面的接触温度。经烧毛后布面应基本无长毛,布面干净均匀,没有条花、划痕。
2 退浆 大多数牛仔布采用上浆染色的经纱与本色的纬纱交织而成,上浆量大,退浆难净,且又是靛蓝染色,色牢度较差,处理不当,极易造成色花、色条及头尾色差。经反复试验,确定采用酶退浆,长车汽蒸水洗法。退浆工艺 浸酶(淀粉酶12g/L,NaCl6g/L,渗透剂JFC4g/L)打卷堆置2h→汽蒸5min→80℃热水洗四道→冷水洗→60℃热水洗三道→冷水洗→烘干 设备 汽蒸水洗联合机 效果 退浆后,织物的浆料残留率应在15%以下,毛效100px/30min。
3 丝光 牛仔布经纬密度大,又有靛蓝染色,因此其丝光工艺与普通印染布既有相同之处,又有不同之处。通过丝光加工,可使面料获得良好的光泽,提高纱线强力及面料的尺寸稳定性。制订工艺时,对烧碱浓度、车速、浸轧烧碱后布面张力、浸轧烧碱的轧液率和丝光渗透剂性能等五个对丝光效果影响最大的因素,要综合考虑。要想获得最佳的丝光效果必须根据不同的产品规格,以及对产品最终性能的要求,对这五个工艺条件进行筛选。
3.1 烧碱浓度 丝光工艺中,碱液温度为常温,为使纤维达到充分润胀的效果,NaOH浓度必须达到一定的要求。在试验中,采用不同浓度的NaOH对牛仔面料进行丝光,通过钡值法测试纱线丝光效果。当烧碱浓度在200g/L以下时,效果不好,随浓度增加,钡值增加,丝光效果变好;但当浓度高于240g/L时,丝光效果增加幅度不显着。综合考虑各种因素,在大机生产时烧碱浓度采用240g/L。
3.2 丝光渗透剂 在丝光过程中,纱线表面的纤维优先润胀,并在每根纤维的周围产生挤紧效应,尤其在张力下这种现象更为明显,妨碍了烧碱液向纱线内部的进一步渗透。因此,需在整理液中加入丝光渗透剂,其性能以及用量,对丝光效果的均匀性影响极大。本试验选用了不同厂家的五种丝光渗透剂,并测试了6、8、10、12g/L渗透剂在240g/L浓度的烧碱条件下,帆布的沉降时间。
在烧碱浓度为240g/L时,渗透剂B和D的效果相当,但综合考虑成本及其它因素,大机生产中选用渗透剂B,用量为10g/L。1.3.3 轧余率、车速以及浸轧烧碱后布面张力的确定 轧余率、车速和浸碱后表面张力同样是丝光工艺中需要考虑的因素,生产中要根据品种作出调整。
4 水洗 丝光后,织物布面残留有较多的烧碱,需进行中和水洗。为了保证充分去除残余碱,并节约用水,通常先采用酸洗中和、再水洗。具体是先浸轧2g/L的冰醋酸进行中和,然后连续通过温度为60℃的温水4槽,30℃的冷水4槽,烘干后布面pH值调至6.0~7.5。
5 定形整纬 丝光水洗后,织物幅宽与纬斜需要在定形机上校正处理。牛仔布产生纬斜是由于纱支较粗,在织制斜纹组织过程中产生的内应力在水洗后处于松弛状态,内应力释放的集中反应,因此必须进行拉斜抗扭。根据生产经验,在完全松弛状态下采集小样,进行充分水洗,使潜在的纬斜应力完全消除,根据所测倾斜度作为整纬的依据,幅宽的确定也同样以水洗后纬向缩率-3%来控制。因此织物在上定形机前,必须认真做好小样测试,以确定织物的幅宽和整纬数据。定形温度一般为100℃,车速以落布九成干为主,从而为后面的预缩工序打下基础。
6 预缩 不同品种的潜在缩水是不同的,即使是相同组织结构和染色方法的牛仔布,由于其棉纱制造工艺及生产条件等不同,其潜在缩水也有较大的差异。因此,必须在定形后取小样进行缩水试验,从而确定预缩量。
7 成品 成品规格 340g(12oz)283/197150~3800px。缩水率 经-1.2%,纬-2.8%(按AATCC标准测试)。成品风格 布面纹理清晰、组织紧密、色泽纯正、光泽度好、手感挺滑。
七 . 后整理中的定型工序对针织物斜纹扭骨的影响
我们都知道,后整理中的定型工序,在某程度上可控制织物之斜度及扭骨,当织物染色后,经脱水,干布,到定型前,可量度其斜纹多少,再按其斜度比例设定其斜纹入机之条件,并可预知其扭骨情度。
圆筒布中抽去一针,形成布面一行空线圈,染色后此行空线圈在圆筒布上的一边纵斜至另一边,而且作螺旋型而上,如不依此空针位开幅,顺圆筒布边开幅顺定,此布扭度为零或接近零,但织物布面线圈存在斜纹。
相反,如按空针位开幅,左右布边出现斜度,而定型时按此斜度作合理取值,斜纹入机作修正定型,但织物相应地存在内张力,当洗水后残余张力释出成扭力,令织物扭曲。
现时市场上一般要求扭度在5 %以内,有些客要求3 %以内,而斜纹在10 %以内,有些客要求8 %以内,两者之标准,定型工序祗能按实际情况在标准范围内修正。以实际成衣方面考虑,高支纱织物布身薄,用幼针织线圈细,布面线圈斜纹不易察觉,对斜纹要求应可低些,扭骨要求则高些。相反,低支纱织物布身厚,用粗针织线圈大,布面线圈斜纹很易察觉,对斜纹要求应可高些,扭骨要求则低些。
斜纹扭骨改善方法,除上文所提及之各项影响,可作一些预防,如用一些捻度较低之纱,低支纱尽量以马克隆值高之棉花纺为合,或将棉纱作蒸纱处理,亦有少许帮助,织机选用要配合织物,疏密度的注意等等,任何可降低总体歪斜的方法,均作考虑。
目前最有效的方法是采用合股纱,或用S及Z捻向的棉纱作隔口交替织入,但客人要接受布面效果才可,或采取后整用树脂控制方法。Z与Z合股加捻2.5T.P.I.,股线为S捻,歪斜17.0,歪向=右。
Z与Z合股加捻6.5T.P.I.,股线为S捻,歪斜11.3,歪向=右。
Z与Z合股加捻12.5T.P.I.,股线为S捻,歪斜0.0,歪向=无。
Z与Z合股加捻14.5T.P.I.,股线为S捻,歪斜3.5,歪向=左。
以上结果,S与Z平行卷绕不加捻,捻向互相抵消,祗余少量歪斜。Z與Z雙紗織布,歪斜最大。Z与Z合股加捻12.5T.P.I.,股线为S捻,为合理之股线捻度,所以歪斜0.0,歪向=无。超出合理捻度,微趋向左。
八 . 后整理的作用是什么?
机织物、针织物及其他各类织物,经过前处理、染色或印花等工序加工后,由于受湿、热、张力等作用,其织物原有门幅、长度等都会产生一定的变形。后整理的目的主要为解决以下几个方面的问题。
◆使织物门幅整齐、尺寸形态稳定。属于此类整理的有:定幅、防缩、防皱和热定形等。
◆改善手感。这类整理可采用机械方法、化学方法或两者共同作用下处理织物,使织物的手感,如柔软、丰满、平滑、硬挺、轻薄、厚实等获得提高。
◆改善织物外观。以物理机械或化学方法增进织物的外观,如光泽、白度、悬垂性等。这类整理有:轧光、电光、增白、缩呢等。
◆提高织物的服用性能,或赋予织物特殊功能。采用机械作用或化学方法使织物表面产生绒毛,增进保暖性,如起毛、剪毛、仿毛、仿真丝、仿麂皮等。采用某些化学药品,使织物具有拒水、拒油、防污、卫生、抗紫外线等特殊功能。化纤织物的亲水、抗静电、防起毛起球等整理。 织物整理的要求,不但因组成织物的纤维种类而异,而且即使是同类纤维组成的织物,也因织物的类型及专门用途的不同,而有一定区别。
根据上述要求,织物后整理加工方法可分为两大类,即机械整理与化学整理。前者通常利用湿、热、力(张力、压力)和机械作用来完成加工方法;后者利用化学药剂与纤维发生化学反应,改变织物的物理化学性能。但二者并无截然界线,例如:柔软整理既可用一般机械方法整理,也可用添加柔软剂方法获得整理效果,但大多是采用两种方法同时进行,如耐久电光整理,使织物先浸轧树脂整理剂,烘干后再经电光机轧光、焙烘而成。
织物整理的内容十分广泛,而且随着科学技术的发展正在不断增添新的内容。目前,织物整理已从单纯地发挥纤维固有特性,以及获得暂时性整理效果的阶段,向着运用新型整理剂和新型设备、赋予织物更加优良和持久效果的方向发展。纺织品通过后整理后,不仅能提高产品档次,同时也提高了产品的附加价值。
因此,后整理的国际前沿水平并非单纯研究其整理技术水平的高低,而应从产品所达到的水平为标准。同时为贯彻环保条例,后整理产品必须符合环保法规,实施清洁生产。
九 . 纺织品染色牢度不合格产生原因和克服办法
1、产生原因 造成染制品染色牢度不合格的原因很多,下面对常见原因作一些分析。① 与染料的结构和性能有关。一般说蒽醌染料、酞菁染料、硫化染料中的硫化元、硫化蓝及金属络合染料等的日晒牢度都比较好。大多数不溶性偶氮染料的日晒牢度也比较高,而联苯胺型的偶氮染料的日晒牢度较低,三芳甲烷染料一般都不耐晒。② 与纤维的种类有关。同一染料在不同性质纤维上的日晒牢度有很大的差异,例如靛蓝在羊毛上能耐晒,而在纤维素纤维上的日晒牢度却很低。又如,粘胶纤维和棉纤维同属纤维素纤维,但凡拉明蓝盐B在粘胶纤维上的日晒牢度比在棉纤维上高得多。③ 与染料浓度有关。同一种染料在同一品种的纤维上,日晒牢度随染料浓度而变化。一般浓度低比浓度高时的日晒牢度差,这种情况在不溶性偶氮染料中更为显著。④ 与外界条件的影响有关。空气含湿量的高低、气温的高低对日本牢度影响很大。一般在含湿高的情况下,日晒牢度较低。凡拉明蓝在南方比在北方地区容易泛红、褪色,空气含湿的高低及气温的变化可能是重要原因。① 与染料的选用有关。染料按水溶性情况可分为水溶性染料和不溶性染料。水溶性染料,如直接染料、酸性染料,若染色后其溶解性能示改变,则上染于织物的染料尚可溶解于水,因此筇洗牢度一般较差。水溶性较差或不溶性染料,如还原染料、硫化染料、不溶性偶气氮染料等,皂洗牢度一般都比较高。活性染料与纤维发生共价键结合时,其皂洗牢度较好,而有未和纤维发生反应的活性染料及水解染料着在纤维上时,皂洗牢度就很差。② 与染色工艺有密切的关系。染料染着不良,浮色多及染后水洗、皂洗不良导致良皂洗牢度的下降。③ 皂洗牢度与日晒牢度不同,染色充分的性况下染色浓度对皂洗牢度的影响较小。④ 皂洗牢度与皂洗条件,如温度、PH值、搅拌情况等有关。① 摩擦牢度与染色工艺有密切的关系。染料渗透均匀,与纤维结合好,表面浮色除得净,则摩擦牢度可以提高;反之,摩擦牢度就下降。② 染色浓宽常常影响摩擦牢度。染色浓度高时容易造成浮色,在单位时间及单位面积内掉下来的染料数量常较浓度低时为多,故摩擦牢度较差。① 与选用的染料本身性有关。如每种分散染料均有其升华牢度,也称为干热牢度。各染料的升华牢度不一样,尤以低温型分散染料牢度最差。② 与染色后热处理的工艺条件有关。分散染料上染织物需经过热溶、焙烘、热定型等高温处理,如温度掌握过高,分散染料易由固态转化成气态,造成原来溶解于纤维中(或固着于纤维上)的染料分子部分升华,造成染色成品色泽的差异。(1) 提高染色牢度,关键在于合理选用染料。染料在织物上的各项染色牢度均要通过试验,做到心中有数。可根据染色产品不同用途,对染色牢度的不同需求,正解地选用染料。(2) 要正确掌握染色工艺,保证按工艺加工,保证染料的织物上的良好扩散、固着,染后充分水洗、皂洗,减少浮色,以保证染色牢度的提高。对于皂洗牢度、摩擦牢度不合格的染色成品可采取重复不洗、皂洗工艺,以去净浮色,提高染色牢度。在分散染料热溶染色等高温处理过程中要严格掌握温度。对熨烫牢度有要求且经高温易变色的产品,织物在染色后需经高温后处理工艺,以提高染色牢度。(3) 染色时如采用水溶性染料,宜采用固色剂和处理等方法,以改变染料的水溶性,提高染色牢度。(4) 要慎重选择助剂,使用的助剂不能影响到各项牢度。(5) 要正确掌握染色牢度试验的各项条件,严伤口按照染色牢度有关规定进行试验,保证各项染色牢度测试数据的正解性,避免错判、误判。
十、弹力针织物产生折痕的原因和解决办法
针织物的染整工艺过程,目前还是以间歇式为主的生产方式。工艺路线长,加工工序多,控制不好很容易在生产过程中形成折痕现象。尤其是现在市场上销售的大多是含氨纶的弹力针织物,由于氨纶的高延伸性(500%~700%),高弹性回复率(200%伸长,95%~99%),更易在生产工艺流程中产生新的折痕问题,有些还是不可修复的折痕,给成品的外观质量带来影响,个别的还要赔偿,工厂因此造成不必要损失和影响。本文针对生产现场常见的一些新的折痕现象、产生的原因及预防措施进行一些归纳总结。
关于折痕的成因,一是针织物的组织结构是由线圈圈套而成,在织造过程中受到张力而产生较大的拉伸变形或生产过程中人为的牵拉;二是织物在染缸内的折叠和挤压,遇上升降温速度过快,纤维在短时间内的收缩差异,导致线圈的移位和变形;三是成品定形后布面温度依然很高,冷却不够形成布车内热压变形;四是因氨纶的弹性回复率比其他纤维高,一经牵拉连带其他纤维一起收缩,引起织物组织结构的变化,再经折叠挤压形成。 织布折痕是指织布后形成的折痕。主要包括压边线折痕、布头布尾折痕和两布边折痕。这些折痕现象应该在坯布初检时加以注意,应及时发现、及时提报。 坯布在织造成卷时,若采用方型撑布架卷取时,会在对折处形成两条从布头到布尾的折痕。产生的原因应该是织物对折由卷布罗拉挤压的结果,其中一条会在剖幅机剖开后消失,另一条则残留在坯布中间,称之为压边线折痕。 解决压边线折痕最好的方法就是采用自动开幅平幅卷取的方式,现在新型的大圆机都有自动开幅平幅卷取装置,有些工厂在方型撑布架卷取落布后再用剖幅机剖开后平幅卷取,也能较好地避免压边线折痕的形成。 自动开幅平幅卷取虽然很好地克服了压边线问题,但操作不当还会造成布头布尾的折痕。布头卷取时一定要平整,最好是两人一起将布头充分理平后再开机,因为一旦布头褶皱或扭曲打卷,松布后会在布头十几码处可见明显的折痕。若此布落布后堆码重压日久还会造成布面压痕,甚至压伤。有些工厂为了减少布头折痕,在卷起纸管或胶管上刷上或贴上黏胶剂或黏胶布,尽量让布头平整卷取。布尾落布后还应将两布边布尾与下层充分展开打结,可以避免布尾松弛状态下形成折痕现象。
另外,坯布卷取时最好使用胶管,可以确保卷取质量又能重复利用,符合环保要求。因为纸管硬度差,受压后易变形或断裂使布面形成新的折痕、压痕或压伤,且受潮后的纸管还会造成坯布沾污。
氨纶含量高的产品,象双面纯棉、厚色丁布等,还会因氨纶的回弹性大,在坯布的两边形成折痕现象。一般这类产品不用水洗,需要先松布再预定形。应注意尽量减少松开坯布在布车内的停放时间,及时预定形,防止坯布布边卷曲堆放时间过长而加重折痕现象。有些织布厂在坯布初卷时因布头没有充分展开,向内卷曲两布边已经形成折痕,应及时向客户提报,避免日后责任不清。 对于一些不用水洗只需要预定形后染色的来坯要求先安排松布。松布这个词,形象地概括了加工的生产工艺过程。松,就是用机器把打卷后的织物松开,为预定形或染色进缸做准备,又必须是松式的处理过程。从中可以看到,松布的机器和工艺操作方法影响着松布的布面效果,控制不好很容易在松布阶段带来布面的折痕现象。
过去的松布机器是先将坯布放入布斗内,然后由上下两个相向运行的橡胶辊牵拉送入摆布架后,落入装布车内。织物完全是强拉硬碾被动松开的,坯布表面的折痕清晰可见,为此,对松布机进行了改造。首先,给布斗加装了可调速电机,由积极输送代替了被动牵拉的方式;另外,松布架平行安装了两个橡胶导布辊,通过可调速电机控制运行,织物完全在松式的状态下松布,彻底解决了因机器带来的布面折痕现象。
机器的问题解决后,关键是如何规范操作,即松布斗可调电机的运行速度与松布架导布辊速度的协调问题。要求操作工注意观察松布后的布面情况,尽量保持松式状态,不要出现人为的拉伸现象。班组长要经常检查员工的现场操作和布面效果,对违反操作要求的应及时处理和扣罚。 化纤类弹力针织物预定形前都要进行前处理水洗,现在大多采用平幅水洗工艺。一方面可以消除织物在织造过程中存在的残余应力,去除织布和整经时的油渍、污脏,防止油污预定形时固着在织物表面,染色时难以清除而影响成品质量;另一方面,还可以提高织物的手感、光泽、渗透性、柔软性等。采用平幅水洗设备进行前处理水洗除油,其中水洗进布方式、展布罗拉运转状态、水洗后布面温度及堆布量大小是造成水洗折痕的主要因素。
前面说过,加工含氨纶的弹力针织物不能有机器和人为拉伸。最先生产的平幅水洗设备,松布与导布辊之间没有设置可调速装置,必须十分小心地松式处理,才会避免折痕现象。生产现场经常出现水洗机松布装置与导布辊不同步,牵拉挤压后造成布面折痕。现在增加调速装置后很好解决了这一问题。
平幅水洗机的展布罗拉,常常会因为轴承故障或皮带打滑,影响展布或扩幅效果,在水洗落布时可见明显折痕现象。要求操作工经常检查进布前展布罗拉以及水洗机各单元转鼓前展布装置运行状况,密切注意水洗后的布面效果,一旦落布发现折痕异常而进布前没有,应及时剪断停机通知机电人员检修或更换机台。
平幅水洗二槽精练温度在98℃以上,后进入80℃左右温洗一次,酸洗中和一次,最后是冷洗。要严守工艺纪律,不要随意将车速调快,防止布面带液温度过高热压后产生的折痕。水洗后的坯布应尽快安排预定形,不要在布车内堆放过多、过高、过久,一来避免因水洗不净造成流色;二来此时布面的可塑性依然较大,有些布两边还呈卷曲状,会因压力的增加在布车内形成新的折痕。 预定形是生产弹力针织物的关键工序,其主要目的除了消除和改善织布带来的拉伸变形、稳定线圈的结构,使织物表面平整无折痕;还可以减轻和防止在染色过程中形成新的折痕现象。织物在预定形过程中形成折痕的主要因素有:机器的运转状态、预定形温度和时间、布面平整度的控制。
实际上,织物表面的折痕现象都是加工过程中的机器或人为操作不当引起。预定形的机器故障也会造成布面折痕现象。比如,进布前的分布档开口位置应适当放大一些,开口太小坯布受到挤压,布面很容易形成折痕;坯布进入轧辊前的展布罗拉是否运行正常,皮带若日久打滑不能将坯布充分展开折叠而经过轧辊碾压也会产生折痕现象。在拉幅定形机超喂区间中空位置,过去是固定两条不锈钢架托住织物,坯布在表面被动拖过进入烘箱,常常发现预定形后经染色成品定形时可见两条明显拖印,影响了布面效果。后改进为由电机带动输送导带,变被动为主动的积极输送方式,很好地解决了这一问题。
前已述及,预定形的目的主要是消除织布和前处理过程中产生的折痕。同时,还能改善纤维非结晶区分子结构的均匀度,保证尺寸的稳定性,防止染色缸内湿热作用后布面折痕或卷边引起的边浅现象。生产实践证明,预定形效果决定成品布面的平整度和布幅稳定性,而预定形的温度和作用时间是影响布面折痕和尺寸稳定性的主要因素。只要控制好预定形工艺,打好基础,成品定形就能有好的效果。预定形温度选择一般倾向在不影响织物弹力和手感的情况下,可以略高一点,尽可能的在预定形时把织物幅宽和布面平整度稳定下来,预防后工序的布面折痕或卷边现象。而预定形作用的时间与预定形温度成反比关系,温度高车速相应调快一些;反之,则慢。一般涤纶类弹力针织物预定形温度控制在200~205℃,锦纶类弹力针织物选择在190~195℃;车速控制在25~30 m/min。
预定形布面平整度的控制,就是坯布预定形的平方米克质量和幅宽预留问题,实际上就是织物超喂量的控制。根据经验,弹力针织物预定形落幅比客户下单要求幅宽略宽5~10 cm,平方米克质量略大5~10g/m2为宜,不能因为克质量做不到采取大缩码的方式预定形,不管布面平整度的效果勉强做最重,一旦布面形成缩码折痕,就是经染色成品定形后也不会去除。因此,对于一些不能满足客户下单要求的平方米克质量或幅宽的预留,生产现场只能以布面平整度为标准做到最重,万一做不到应及时反馈客户更改工艺参数。 染色缸内造成弹力针织物折痕的主要因素有:喷嘴压力大小和提升辊运转速度;缠车、压缸、堵布;染色升降温速度。
染色过程中染色机喷嘴压力的大小和提升辊运转速度快慢之间的配合与协调是染色操作工根据工艺实践、针对不同布种进行控制和熟练掌握的。对于厚重织物染色机的喷嘴压力应适当调大一点,提升辊速度则放慢一点,这样才能顺利推动织物正常运行;而轻薄织物则相反,需要将喷嘴压力适当调小,提升辊速度增加一些,减小水流量与提升辊和织物之间受到的张力,从而减小染缸内织物表面拉伸而造成的折痕现象。
染色缸内的缠车、压缸、堵布引起的布面折痕一般由以下几个原因造成:一是投染缸量过大,浴比小,织物在缸内循环周期长,相互折叠、挤压,布面很容易生成鸡爪痕或折痕。染色排缸一定要注意缸量大小,一般按容布量的60%~70%安排生产,避免缸内织物运行不畅造成的折痕现象;二是织布的断纱或进缸前接头不牢引起的断布堵在缸内,长时间在高温条件下、加上水冲形成的堵布折痕。要求操作工坚守岗位,注意观察染缸内坯布运行状态,尽早发现,及时处理;三是湿强度比较差的再生纤维素纤维,如莫代尔、黏胶纤维、竹纤维织物,在染缸内加色、修色时间过长引起断布,造成的压缸折痕;这类产品剪样对色,发现颜色相差较大时,应先水洗出缸,套色接近后再进缸染色;色花严重的协商客户改为深色,尽量不要采取剥色后回修,以避免纤维湿强度差而在缸内断布现象。
染色过程的升降温速度,不仅影响染色的匀染性,而且还制约染色后织物的手感和布面折痕程度。热加工温度若控制不当,造成织物表面温度聚热或聚冷,会因纤维热收缩引起布面折痕。生产实践中曾经出现过,因操作工违反工艺规定将升降温由计算机自动控制改为手动后,出现的布面折痕现象,有时甚至是严重的折痕。所以,染色过程严格按计算机程序,采取缓慢升降温不但有利于匀染,还有利于减少布面折痕。因此,强化员工工艺纪律教育,对控制染色过程的折痕很有必要。 经过预定形后的弹力针织物,成品定形严格的说只是烘干的过程。目的是消除染色缸内因热收缩带来的布面折痕,重新赋予织物表面光洁度和平整度以及客户下单要求的幅宽和平方米克质量。但也要注意成品定形温度、定形机运行状态、特别是成品定形后布面冷却效果以及成品在布车内叠放堆码,,控制不当,也会造成布面新的折痕现象。
弹力针织物在预定形阶段就采用了比较高的定形温度,对后工序染色湿热加工可能形成的折痕起到很好的预防作用。所以,成品定形温度的选择比预定形要偏低5~l0℃,棉类或再生纤维素纤维类会更低一些,约低l0~30℃。根据经验,成品定形后的布面效果是随定形温度提高,折痕少而轻的,少数染缸内折痕明显的,可以适当提高成品定形温度而有所改善。
成品定形时操作工应注意观察机器的运行状态,防止织物跑偏、脱针或展布罗拉异常造成的纬斜甚至折痕现象。落布还要视布面平整度及客户下单幅宽、平方米克质量情况及时调整织物的伸缩码,避免成品定形异常带来的布面折痕。
织物经过热定形后,应以适当的速率进行冷却,如果冷却速率太慢,对生产来说是不适宜的。如果冷却区不够长、车速过快或达不到冷却效果都可能引起织物产生折痕。
根据现场测试,如果成品定形温度设定为200℃,织物在车速300frain,经过了9节烘箱,在出口处布面温度有170~is0℃,再经过冷风区和冷却辊筒后布面的温度仍然在60℃以上,此时若落布折叠热压,很容易产生布面折痕现象。
目前,拉幅定形机冷却方式主要有两种:一是吹冷风;二是经过冷风区后进入冷水辊筒,织物通过接触冷水辊筒表面降温。但是,从实际运用来看落布后的布面温度,达不到冷却效果。因此对冷却辊筒降温系统进行了技术改造,给冷却辊筒做了特殊降温处理,辊筒表面温度可控制在4℃左右,成品定形后织物经过冷风区进入冷却辊筒表面处理后,布面温度已降至50℃以下,对改善布面的折痕现象起NT明显的作用。成品定形后的堆放方式也很重要。后机操作工一定要有品质意识,织物落在布车内应始终保持平幅状态,量幅宽、打克质量后应用两手平放在布车内,杜绝随意扔、甩、乱放现象,避免人为造成的布面折痕。成品包装是弹力针织物染整加工过程中的最后一道工序。包装质量控制不好,同样也会造成布面新的折痕现象,使得染色和定形所有努力前功尽弃。影响包装质量的主要因素有:纸管的硬度、卷布的操作方法。7.1 纸管硬度 以来料加工为主的染整厂,成品是以卷取的方式送客户。所以,卷取纸管的选用很有讲究,纸管要求饱满、圆挺,垂直度要好且要有一定的硬度和强度。饱满、圆挺可以确保卷取时布面平滑无折痕;一定的硬度和强度才能抵抗在运输过程中的搬、扛、压,防止里面的纸管变形或折断后布面形成压痕和折痕。卷布最重要的是初卷,织物卷取在纸管上时两手一定要充分将布理平,不要随意折皱或扭曲。先将布头切齐,叠放不要过多、过松,卷布机车速起步要慢,在确保布面平、匀,布边整齐后才能缓慢提速并要一直保持匀速运行。 要减少和克服弹力针织物的折痕问题,必须在整个染整生产过程中,念好“松、查、严”三字经:“松”,就是要在本工序加工的机器上尽量减少张力,保持松式的处理过程,这是确保所生产成品无折痕的需要。“查”,就是要检查客户的来坯情况,是否有因卷布方式不当带来的坯布折痕;检查本工序加工过程是否有因设备故障或违规操作造成的布面折痕,要求及时发现,及时处理。“严”字当头,严把品质关,严格按工艺操作规程办事,严厉扣罚和处理违规操作带来的布面折痕异常。只要各生产环节都来重视“松、查、严”,预防和克服布面折痕的基础工作就有了保证。
十 一. 精练剂的应用性能测试
精练剂的主要功能是帮助液碱渗透到纤维、纱线内部,促使蜡状物,油脂类物质,和杂质残浆的乳化、分散、清除,对合成纤维中的油剂,浆料的去除。因此精练剂除了有较好的净洗效果外,更需有渗透、乳化、分散、增溶等效果。因此评估精练剂的优劣,要测试其与化学药品(氢氧化钠、双氧水等)的相容性,耐硬水性能,又符合设备要求的起泡性,并对纤维的亲和力要小,易快速洗净,防止再沾污等性能。
通过测定精练剂的性能及效果测试实验,对所用精练剂的性能进行综合判断。学会判定精练剂的优劣。
1、通过精练剂的性能及效果测试实验,知道精练剂在前处理加工中的作用;
2、通过精练剂的性能测定试验,学会判定精练剂优劣的方法。
精练剂品种很多,有精练退浆剂、精练除油剂、精练渗透剂、合纤精练剂、低泡精练剂、浓缩精练剂、氨纶去油精练剂、染色同浴精练剂等等。它们应用于各厂的生产设备、工艺条件也都不一样,因此精练效果的评估方法也各不相同,一般可分为一般精练剂工艺条件和耐碱精练剂工艺条件二大类。
(1)织物: 纯棉针织布(21s,160-220g/m2)
(2)精练浴处方: 双氧水(27.5%) 5g/L
(3)精练工艺: 精练(98℃/45分钟)→冷水洗→晾干。
(1) 织物: 纯棉纱卡(长车浸轧,21s×21s,108×58)
(3)漂白浴配方:双氧水(27.5%) 15g/L
(4)长车前处理工艺:煮练(二浸二轧,轧余率80%)→汽蒸(90分钟)→漂白(二浸二轧,轧余率80%)→汽蒸(45分钟)→热水洗→冷水洗→晾干
经过上述精练工艺的条件处理后的试样布,评定其精练效果,一般有三种方法:Ⅰ、毛细管效应的测定;Ⅱ、白度的测定;Ⅲ、残脂率的测定。
毛细管效应的高低,直接影响后加工的质量。织物毛细管效应的测定也就是测定水在织物上的扩散速度。有三种方法:⑴定时法,以一定时间上升的高度;⑵定高法,上升一定的高度所需的时间;⑶水滴化开法;工厂多用定时法和水滴化开法。
(1)定时法:
① 仪器:毛细管效应测定仪,该仪器安装在3个调整水平的螺丝钉上,座盘上放有盛液槽,其上方设横架,横架上有夹子4个,在夹子边上各装有垂直的、具有毫米刻度的标尺。
将待测布样剪成经向750px、纬向125px的布条2块,在离一端25px处沿纬向用铅笔划一线水平标记,划线下有夹子夹住作为重荷。测定前,在盛水槽加入约2立升蒸馏水。调整仪器水平、调整液面与标尺读数零点对齐。然后升高横架,将试样布条上端用夹子固定在横架上,并使其下端的铅笔划线正好与标尺读数零点对齐。再将横架连同标尺和试样一起下降,直到标尺读数零点与水平面接触为止,并立即开启秒表开始计时,记录30分钟时液体上升的高度(cm)。如液体上升高度参差不齐,应读取最低值。
毛细管效应一般采用定时法,如不注明试验条件,毛效的高度一般是指蒸馏水在室温条件下30分钟上升的高度。
将待试布样在绷紧架上,用滴定管吸取蒸馏水,在距离布面25px处垂直滴下,并立即开启秒表开始计时,当液滴表面的镜面刚好消失时按停秒表,在不同位置测定5—10次后取平均值,水滴消失时间短则毛细管效应好。
2.白度的测定(参照GB 8425 纺织品白度的仪器评定的方法)
白度的测定方法很多,常用有二种:一种是用分光光度测色仪来测定各波长的反射率,通过计算机后得到L值、a值、b值,再通过白度计算式,得白度值。另一种是在白度计上进行测定,用特定的波长光线通过滤光片使透过的波长低于500nm,染整公司采用WSD-3C型白度仪(波长为455nm)测得。注:不同的白度仪所测得数据不完全一致,报告上应注明仪器的型号。
3.精练剂的渗透性能测定:测试方法相同于渗透剂的渗透力帆布沉降法测定(参照HB/T2575)。
精练剂在有些工艺和配制中需要与浓碱一起应用,则该精练剂一定要有良好的耐碱性。精练剂耐碱性能的测定就是在一定的碱浓度下,配制当即和放置24小时后观察其溶液的状态:分为清晰、微混、混浊、悬浮物析出、沉淀析出和表面有无油膜几种。
配液处方:精练剂 35g/L 35g/L 35g/L
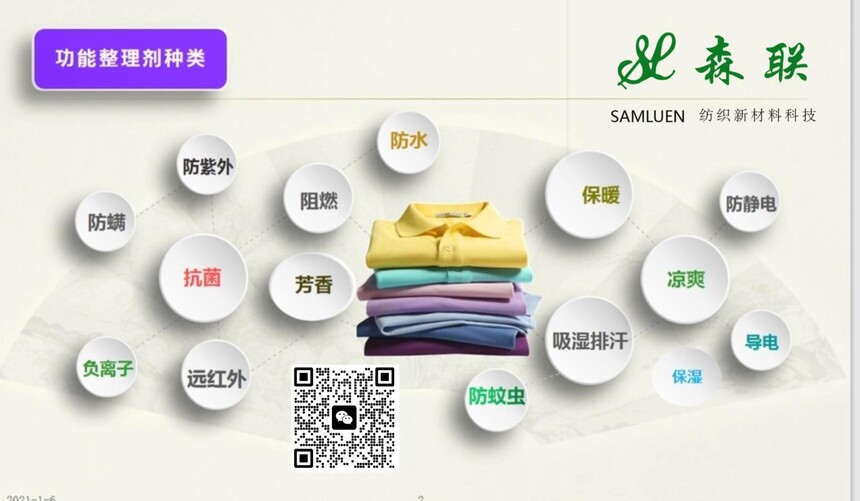